Fired Creations: In Sparkling Form
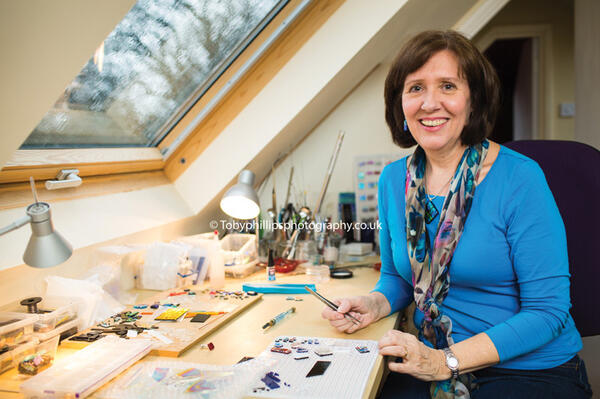
Published 3 March 2015
The British Museum has in its collection a Roman glass cage cup dating back to the 4th Century, called The Lycurgus Cup.
It has been described as 'the most spectacular glass of the period which we know to have existed' because of its use of a dichroic glass, which changes colour in the light. The cup's opaque green colour turns into a translucent red when light is shone through it, and it also contains fragments of colloidal gold and silver, making it an intriguing object for Museum visitors.
Quite how much The Lycurgus Cup would be worth were it was to be sold is anyone's guess. But you can get your hands on far more affordable dichroic glass items at a small stall in the Horsham Market on a Saturday.
Angela Jenkinson creates individual pieces of jewellery and decorations, from the same type of glass for her business, Fired Creations, born in 2005.
Angela said: "I went to a craft fair and was just looking around when I came across someone who sold glass fusing supplies. They had packs of tiny pieces of dichroic glass with instructions on how to use a hand-held blowtorch to melt glass and make jewellery.
"For a few years, I had been making silver jewellery out of precious metal clay (PMC) which has silver elements within it, so you make something out of the clay and you're left with a silver item after firing. I thought that the dichroic glass offered something new, so I bought a packet. A short time later, I went to California and in a craft shop in San Diego I came across a magazine with an article about firing glass.
"This gave me some very useful tips, as I had found it was very difficult to get the right effect with a blowtorch. I decided to buy a new kiln suited for glass and it's all grown from there."
Angela started making small pieces of jewellery including earrings, studs, pendants and rings, for family and friends. But when a friend convinced Angela to support a charity craft fair by setting up stall, she was surprised at how popular her fused dichroic glass jewellery proved to be.
"I think it is popular because it is very colourful," said Angela. "Although on a rainy you can't really see the sparkle, you'll see different colours in the light. Another thing people like is that it is just about impossible to repeat the same look with two items of jewellery. I can make a little pair of stud earrings using exactly the same glass, but it will never be identical. That is the unique selling points of dichroic glass, as you will have a truly individual piece of jewellery."
True Colours
"I tend to buy mixed bags of dichroic glass and play around with different colours and shapes. Sometimes, I come up with weird combinations as there are no limitations really. You can put one colour over another or even several colours over several others.
"You might put red glass on top of a blue glass base and depending on the angle of the light you'll see different colours. It is fun to play around with the effects."
Angela buys the fused dichroic glass by an American company called Bullseye Glass Co, which sells small sheets of the glass in translucent and opalescent styles, in a range of patterns and colours. Whilst popular with jewellery makers and artists across the world, it is a complicated process to make dichroic glass.
It is made up of tiny layers of metal oxides, including titanium, chromium, aluminium, zirconium and magnesium, which are then vapourised at an extreme temperature by an electron beam in a vacuum chamber. The vapour then condenses on the surface of the glass and a protective layer of quartz crystal is added too.
The finished glass is still extremely thin, yet could contain 50 different layers, and because of the variations in the oxides, every fragment offers something different. These small pieces of dichroic glass are then fused by Angela to create jewellery and after multiple firings in the kiln, she will have created a true one-off every time!
Angela said: "You can't always tell what colour it is going to end up being! Sometimes I look at a piece of glass and think 'that's going to come out light green with a hint of gold' and it'll come out dark green. After a while, you do get to know what colour it is likely to be by holding up the glass to the light, but even after ten years, I can be surprised by what comes out of the kiln.
"I do like to work with blues and purples more than anything, as they tend to sell well. The trickiest colour to work with is red, because there is not a true red dichroic glass, and you have to create your own shades of red with base glass.That is what makes it fun – you always get something quite unexpected."
The Heat is On
There are occasions though, when the unexpected surprise is disappointing! On these occasions, Angela may add another layer of clear glass on top or even ditch the item altogether!
It is sometimes better to do this than continuing with what is a time-consuming process. The first firing in the kiln takes about five hours, after which Angela uses a grinding machine to shape the pieces. They then go back into the kiln for polishing, which brings back the shine.
Angela also creates larger items, such as coasters and wall hangings, which take up far more space. She said: "I make wall hangings using two sheets of clear glass with a high-temperature wire which doesn't bend when heated in the kiln, so I can make a hook for it to hang from.
"These are proving quite popular for people who are redecorating bathrooms or kitchens, as these are not affected by moisture. I also make plates and things like coasters too, although the biggest piece I can create is 40 cm because of the size of the kiln.
"That takes about 17 hours to heat, and even then you have to be careful with thermal shock. It can be irritating when you lose a piece after spending so much time on it!"
You can find Fired Creations at Horsham Market in the Carfax every Saturday or visit the website at www.firedcreations.co.uk